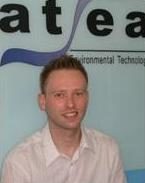
Dipl.-Ing. Christoph Gazda
Diplomprüfung: 04/2009
In Kooperation mit: atea (Shanghai) Environmental Ltd.
The aim of the quenching process is to bring hot gas in thermal equilibrium with water or a special quench liquid. Quench towers are used in the chemical industry for a rapid cooling of an incoming hot exhaust gas. The quench tower cools down hot gases from high temperatures, in this case 350 °C, to a lower temperature, here 68 °C. Normally the hot gas is generated in an incinerator. The areas of a quench which are in permanent contact with the hot gas and quench liquid are eminently prone and endangered to corrosion. These areas require a special collection of material and careful attention to the construction. A typically used material is fibre reinforced plastic (FRP), which is non-corrosive against aggressive chemical substances, like Hydrogen Chloride (HCl) and Chlorine (Cl2), and has also good mechanical properties. Quench towers are needed as a first step, followed by another gas treatment step which normally is to treat the polluted gas in a scrubber.
The goal of this thesis is to develop a FRP quench tower with focus on the critical hot-gas entry and to develop a cooling system by applying a water film onto the inner quench wall.
This cooling system protects the inner quench wall against heat damages, because of the hot and aggressive flue gas. In order that the reader can comprehend this, he will be introduced step by step into the quenching process. In the first chapter the procedure of quenching, and what it is for, is explained. The key statement of this chapter is 'quenching is rapid, shock-like cooling by direct contact between the quench liquid and the incoming hot flue gas'.
It is explained to the reader why it so important to use high-quality materials like Hastelloy and fibre reinforced plastics. Especially the relatively new fibre composite material (FRP) is defined in detail. The lamination structure as well as the choice of the right resins and fibre materials are described.
Furthermore, a complex static calculation of a quench tower, according to DIN 18820 (glass fibre reinforced unsaturated polyester [GF-UP] and phenacrylic [GF-PHA] resin structural composites; Structure, fabrication and properties) is explained in detail by an example.
After the basics of quenching and the corresponding material collection have been brought closer to the reader, it should be more and more clear why a wall cooling system at the hot gas entry is essential.
To test the functionality of the designed cooling system, a prototype with the scale 1:1 was built up,which is shown in the following picture.

Several cases were simulated, such as failure of a tangential nozzle, reduction of the cooling water flow rate, installation of a dam, etc. The result of these test series is a diagram which shows the relation between nozzle diameter and volume flow rate. Further more, the spraying system which is used for gas cooling is explained in detail, especially the function of a full cone spray nozzle.
In this context, thermodynamic considerations are put forward. The basic principle of cooling in a quench tower is cooling by evaporation.
Furthermore, the author describes the process of standardization of FRP quench towers in five steps.
Finally, a view into the future is done, which can be proved or disproved by other prototypes, also experiences and problems which were collected during building up the prototype are described.