Aber was ist eigentlich ein Wertstrom?
Unter "Wertstrom" werden alle Aktivitäten verstanden, die erforderlich sind, um aus den eingehenden Materialien (Input) ein Erzeugnis (Output) zu erstellen. Die Aktivitäten können zunächst wertschöpfend oder nicht-wertschöpfend sein, wobei es grundsätzlich gilt letztere zu eliminieren. Beim Wertstromdesign wird diese Kette der Aktivitäten "stromaufwärts" von den Kundenanforderungen bis zum gelieferten Rohmaterial betrachtet. So wird sichergestellt, dass das gesamte Fertigungssystem auf den Absatzmarkt ausgerichtet ist und bei der Analyse nichts übersehen wird.
Wie läuft das Wertstromdesign ab?
Im Wesentlichen weist der Prozess des Wertstromdesigns vier Schritte auf:
- Bilden von Produktfamilien und Auswahl
- Erhebung des Ist-Wertstroms
- Entwicklung eines Soll-Wertstroms
- Umsetzung der erarbeiteten Maßnahmen
Für welche Produktfamilie soll der Wertstrom untersucht werden?
Die Konzentration auf jeweils eine Produktfamilie verringert die Komplexität von Analyse und Design. Eine Produktfamilie ist eine Gruppe von Produkten, die ähnliche Verarbeitungsschritte unter Einsatz ähnlicher Maschinen oder allgemeiner ähnlicher Ressourcen erfordern. Bei der Identifikation solcher Familien kann die Maschinen-Erzeugnis-Matrix hilfreich sein.
Sind die Produktfamilien identifiziert, sollte eine Rangfolge erstellt werden. Häufig wird diejenige Produktfamilie zuerst bearbeitet, die das größte Potenzial für eine Effizienzsteigerung bietet. Dies lässt sich zum Beispiel am Material- oder am Personaleinsatz festmachen. Bei der Festlegung kann auch die Kategorisierung nach der ABC-Analyse erfolgen.
Wie wird der Ist-Zustand erhoben und erfasst?
Idealerweise wird der Wertstrom händisch mit dem Bleistift aufgezeichnet. Für die Abbildung stehen verschiedene Symbole zur Verfügung, welche weiter unten abgebildet sind. Damit der Modellierer nichts übersieht, sollte der Materialfluss zu Fuß verfolgt werden, und zwar stromaufwärts von Rampe zu Rampe.
Folgender Ablauf der Ist-Aufnahme bietet sich an:
- Abbildung der Fertigungsstufen mit den Datenfeldern (siehe Info-Kasten unten) und Bestands-Dreiecken, welche Bestandsmengen (BM) oder Reichweiten (RW) ausweisen (zur Umrechnung vergleiche das Gesetz von Little)
- Darstellung des Materialflusses mit stromabwärts gerichteten Kanten
- Einzeichnen der Informationsflüsse vom Kunden, zum Lieferanten sowie zu den einzelnen Fertigungsstufen
- Abtragen der Durchlaufzeitenlinie und -daten

Nach welchen Prinzipien erfolgen nun Analyse und Design?
Im Mittelpunkt der Analyse steht das Auffinden von Verschwendung. Sie wird besonders deutlich in Umlaufbeständen und Durchlaufzeiten. Ursachen dafür werden im Ist-Modell mit so genannten "Kaizen-Blitzen" versehen. Sie signalisieren Prozessbereiche, die verbessert werden müssen.
Die schwerwiegendste Ursache für Verschwendung liegt in der Überproduktion. Diese entsteht, wenn mehr, früher oder schneller gefertigt wird als es der nachfolgende Produktionsschritt erfordert. Aus diesem Grund steht bei der Reorganisation die Synchronisierung der Aktivitäten entlang des Fertigungsprozesses im Mittelpunkt.
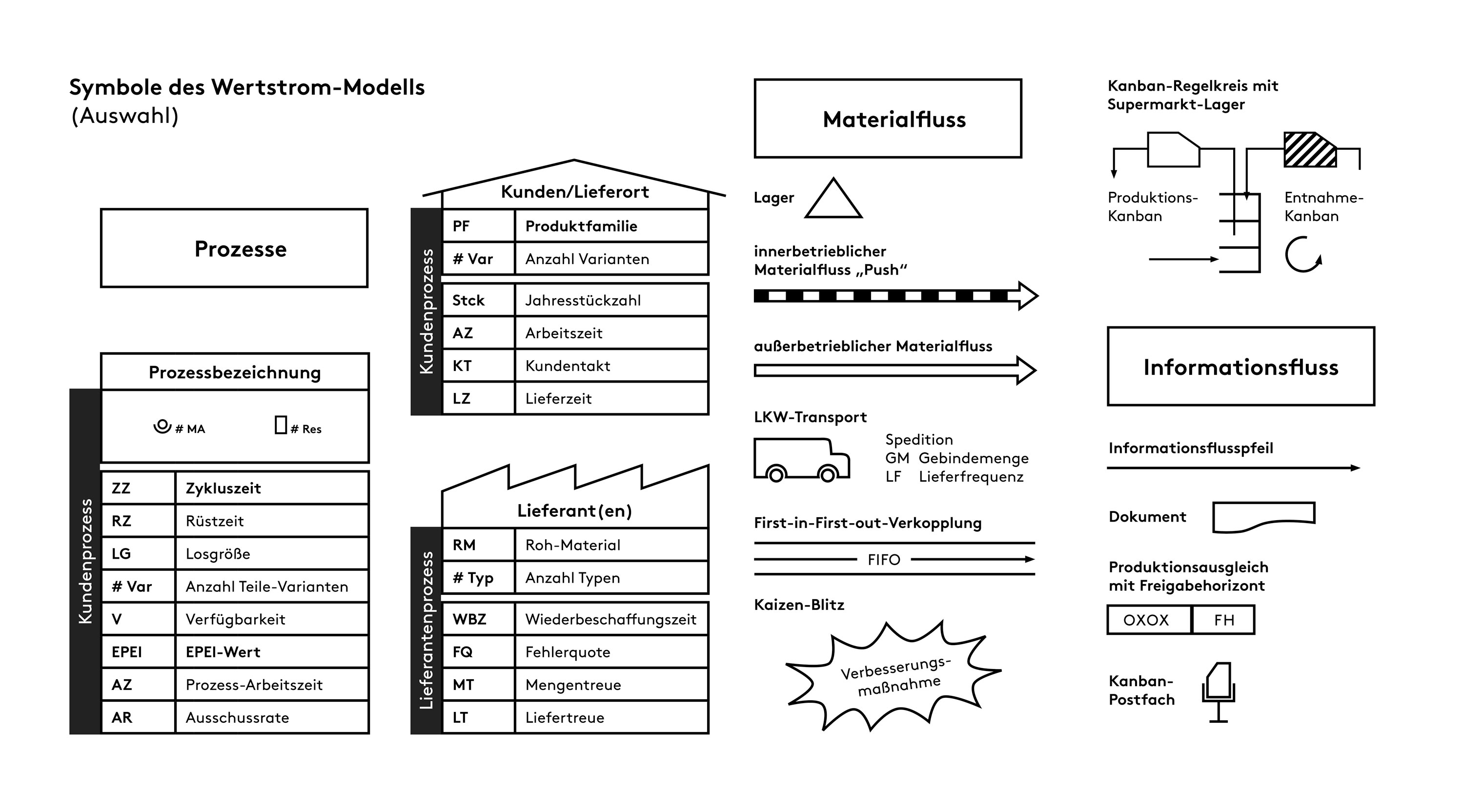
Die Synchronisierung soll nach folgenden Prinzipien sichergestellt werden:
- Berücksichtigung des Kundentaktes: Die Taktzeit ergibt sich aus dem Quotienten von verfügbarer Betriebszeit pro Zeiteinheit und der vom Kunden benötigten Produktionsmenge ("Primärbedarf") pro Zeiteinheit. Mit der Taktung wird versucht, die Produktionsgeschwindigkeit an den Absatz anzugleichen.
- Einführung einer kontinuierlichen Fließfertigung: Soweit möglich sollten die Fertigungsschritte vom Material im Verfahren des One-Piece-Flow durchlaufen werden. Dies setzt eine räumliche Integration sowie eine zeitliche und inhaltliche Abstimmung der Arbeitsstationen voraus.
- Aufbau von selbststeuernden Versorgungssystemen: Dort, wo eine kontinuierliche Fließfertigung nicht möglich ist, sollte der Materialfluss über einen Supermarkt mit Hilfe von Kanbans gesteuert werden.
- Steuerung des Schrittmacherprozesses: In selbststeuernden Versorgungssystemen muss nur ein Fertigungsschritt zentral geplant werden: der sogenannte Schrittmacherprozess. Er liegt meist so weit wie möglich am Ende des Fertigungsprozesses, denn stromaufwärts wirkt der "Pull-Effekt" des Kanban-Systems.
- Ausgleich des Variantenmixes: Für jeden betrachteten Zeitraum (Woche, Tag oder Schicht) sollten alle erforderlichen Varianten gefertigt werden. So kann das Ausgangslager klein sein und auf die Bedarfsschwankungen der Kunden kann schnell reagiert werden (Nivellierung/Heijunka). Der Ausgleich des Variantenmixes wird am Schrittmacherprozess sicher gestellt.
Nach diesen Prinzipien wird der Soll-Prozess grafisch abgebildet. Das Modell wird als Masterplan für die Umsetzung herangezogen.
Datenfelder
Zu den Fertigungsstufen werden Daten erhoben, welche relevant sind für eine Beurteilung des Wertstroms. Sie werden im Prozessbild in Datenfeldern unter den Fertigungsstufen aufgeführt. Häufig werden folgende Daten ausgewiesen (Auswahl):
- Zykluszeit (ZZ): Dauer zwischen dem Beginn der Bearbeitung eines Teils bis zum Beginn der Bearbeitung des nächsten Teils
- Rüstzeit (RZ): Dauer des Wechsels der Maschine von einer Variante zur nächsten (SMED)
- Maschinenverfügbarkeit (V): Anteil der tatsächlich produktiven Zeit an der geplanten produktiven Zeit (Gesamtanlageneffektivität)
- Zahl der Mitarbeitenden (#MA): Anzahl am Fertigungsschritt beteiligter Mitarbeitender
- Verfügbare Arbeitszeit der Mitarbeitenden (AZ): Arbeitszeit abzüglich Pausen sowie persönlicher und technischer Verteilzeiten
- Ausschussrate (AR): Anteil der Schlechtteile an allen produzierten Teilen
Was ist bei der Umsetzung zu beachten?
Aus der Analyse und dem Soll-Modell lassen sich die Ansatzpunkte für eine Reorganisation ableiten. Erforderliche Maßnahmen werden im Team diskutiert und formuliert. Sie sollten in einen Projektplan einfließen, welcher zur Umsetzungsplanung und -steuerung herangezogen wird. Ein*e Projektleiter*in ist zu benennen, von anderen Aufgaben frei zu stellen und mit erforderlichen Kompetenzen auszustatten.
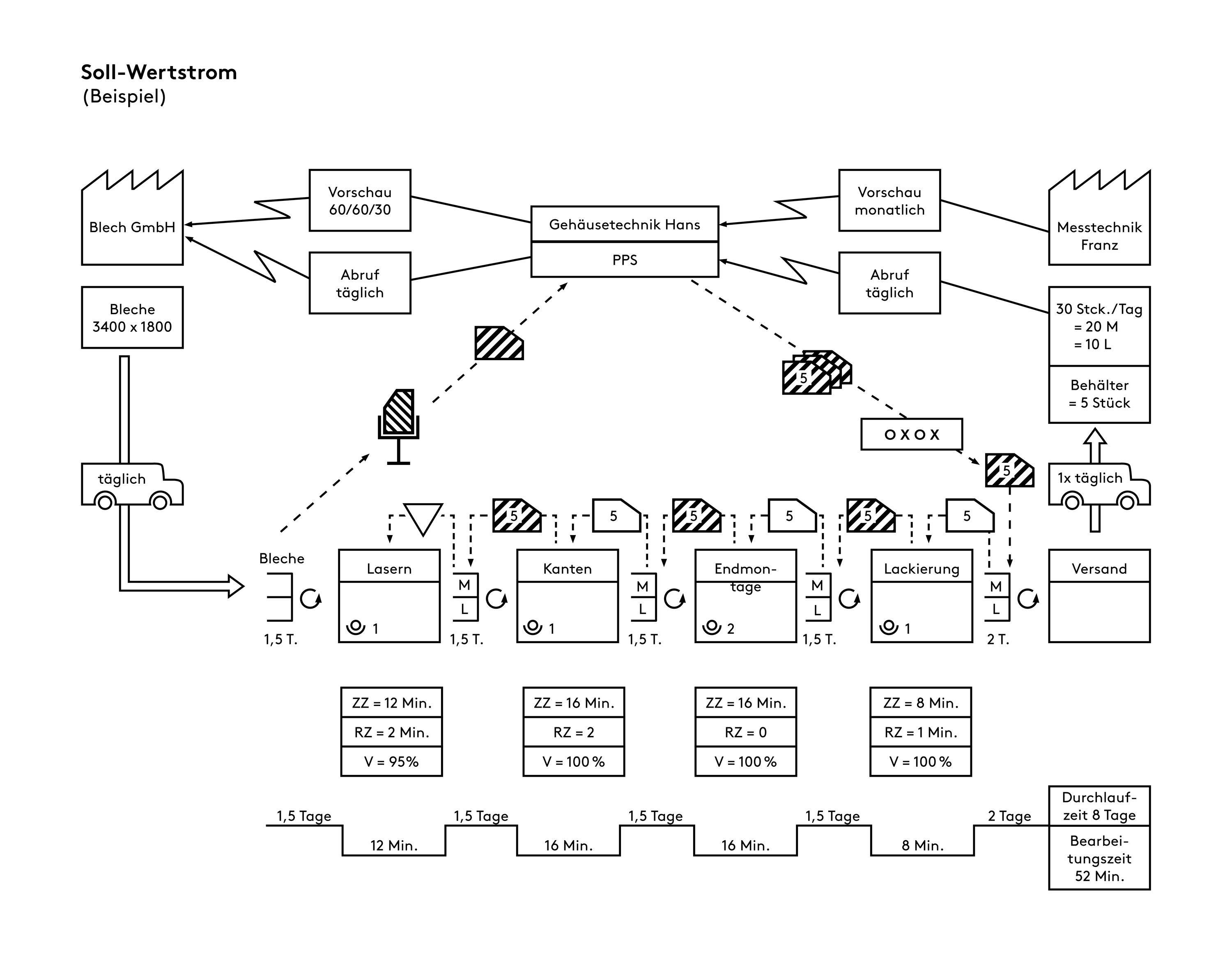